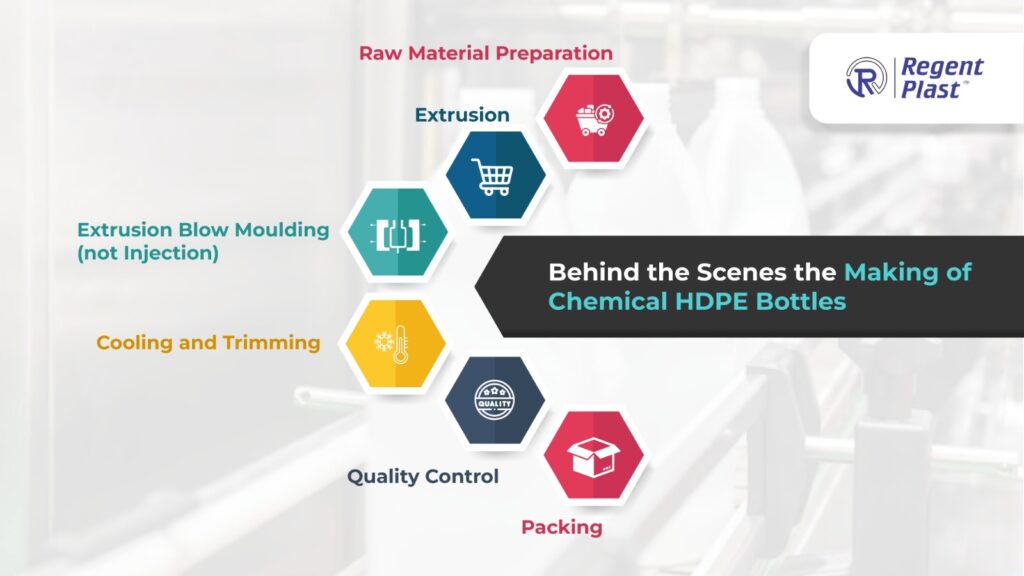
Making of Chemical HDPE Bottles-Behind the Scenes
Have you ever wondered about the sturdy plastic bottles that house a myriad of chemicals in industries ranging from pharmaceuticals to agriculture? The answer lies in High-Density Polyethylene (HDPE), a versatile and durable plastic material that has become the backbone of chemical packaging. In this blog, we’ll take a deep dive into the making of chemical HDPE bottles, exploring their use, need, and the numerous benefits they offer to various industries.
Understanding the Use and Need of HDPE Plastic Bottles
1. What is HDPE?
High-Density Polyethylene (HDPE) is a type of thermoplastic polymer with a high strength-to-density ratio. It is known for its toughness, resistance to chemicals, and durability. These properties make HDPE an ideal material for the production of containers, including bottles, used in the storage and transportation of various chemicals.
2. Why Choose HDPE for Chemical Bottles?
a. Chemical Resistance: HDPE exhibits excellent resistance to a wide range of chemicals, making it suitable for storing corrosive substances without the risk of degradation or contamination.
b. Durability: The robust nature of HDPE ensures that the bottles can withstand the rigors of transportation, handling, and storage, providing a secure containment for diverse chemical products.
c. Versatility: HDPE bottles come in various shapes and sizes, catering to the specific needs of different industries. From small pharmaceutical bottles to large agricultural containers, HDPE is adaptable to a multitude of applications.
d. Cost-Effectiveness: HDPE is a cost-effective material, making it an attractive choice for industries seeking a balance between performance and budget considerations.
Manufacturing Process of HDPE Bottles
Now, let’s delve into the intricate process behind the scenes that transforms raw HDPE material into the chemical bottles we encounter in our daily lives.
1. Raw Material Preparation:
The journey begins with the collection of raw HDPE resin pellets. These pellets are typically produced through the polymerization of ethylene, a hydrocarbon gas derived from crude oil or natural gas. The quality and properties of the resin depend on the specific manufacturing process and additives used.
2. Extrusion:
The raw HDPE resin pellets are then melted and extruded into a continuous parison – a tube-like structure with an opening at one end. This process is known as extrusion and is facilitated by heating the resin to its melting point.
3. Extrusion Blow Moulding:
The extruded parison is transferred to a mould, and a controlled amount of air is injected into the parison, forcing it to take the shape of the mould. This process, known as extrusion blow moulding, results in the creation of the bottle’s basic form. The mould dictates the final shape and size of the bottle.
4. Cooling and Trimming:
Once the bottle shape is formed, it undergoes a cooling process to solidify the plastic. After cooling, excess material is trimmed, leaving behind a seamless and uniform HDPE bottle.
5. Quality Control:
Quality control measures are implemented throughout the manufacturing process to ensure that the produced bottles meet industry standards. This includes checks for thickness, dimensions, and overall structural integrity.
6. Packaging:
After undergoing rigorous quality checks, the finished HDPE bottles move on to the packaging stage. To maintain product integrity, bottles are carefully sorted, grouped, sealed, and labelled for identification. By ensuring that the containers are distribution-ready, this procedure helps to preserve their quality throughout storage and transportation. It is the last stage of production, preparing the carefully constructed HDPE bottles to be delivered to customers, where they will be safely used to carry and hold various chemicals used in many different sectors.
Benefits of HDPE Plastic Bottles in Chemical Industries
1. Chemical Compatibility:
HDPE exhibits exceptional resistance to a wide range of chemicals, making it an ideal choice for packaging chemicals such as acids, bases, and solvents. This ensures that the integrity of both the container and its contents is maintained, preventing leaks, spills, and contamination.
2. Lightweight and Durable:
HDPE bottles are lightweight yet durable, making them easy to handle and transport while providing robust protection for the chemicals they contain. This characteristic is particularly crucial in industries where ease of handling and cost-effective transportation is paramount.
3. Environmental Considerations:
HDPE is a recyclable material, contributing to sustainability efforts in reducing plastic waste. Many industries are increasingly adopting recycling programs, allowing used HDPE bottles to be transformed into new products, reducing their environmental impact.
4. Versatility in Design:
The versatility of HDPE allows for the creation of bottles in various shapes and sizes, catering to the specific requirements of different industries. Whether it’s a small pharmaceutical vial or a large agricultural container, HDPE can be moulded to suit diverse applications.
5. Cost-Effective Packaging:
The cost-effectiveness of HDPE makes it an economical choice for packaging in chemical industries. Its affordability, coupled with its performance characteristics, makes it a preferred material for businesses seeking to balance functionality and budget considerations.
Conclusion
The making of chemical HDPE bottles is a fascinating process that involves transforming raw HDPE resin into versatile containers that play a crucial role in various industries. The use, need, and benefits of HDPE plastic bottles in chemical applications underscore the importance of this material in ensuring the safe storage and transportation of diverse chemicals.
As we continue to navigate the complexities of modern industry, understanding the behind-the-scenes processes that bring everyday items like HDPE bottles to life enhances our appreciation for the advancements in material science and manufacturing technologies. In an era where sustainability and functionality are at the forefront of industry considerations, HDPE stands as a testament to the innovation driving the evolution of chemical packaging.